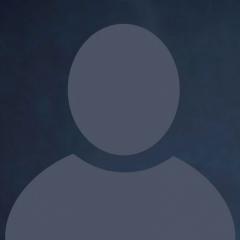
About
Dr. Latorre’s research has focused on the hydrodynamics and structural design of 30-50 knot large passenger/cargo vessels. At the International Conference FAST 2003 held in Ischia (Naples) Italy Oct. 2003, Dr. Latorre moderated the hydrodynamics session and in the design session presented a paper on the design of a 40 kt cargo carrying trimaran utilizing micro-bubble drag reduction on the side hulls. This design is based on a patented idea developed by Dr. Latorre and his colleague Richard Philips at the US Navy Underwater Warfare Center in Newport Rhode Island. He also has published articles on microbubble drag reduction on a model SES in Ocean Engineering as well as drag reduction from using self polishing hull coatings in the Journal of Naval Engineers.
These R&D projects have been organized into a 3 credit NAME 4177 elective course Advanced Marine Vehicle Design. NAME 4177 includes a review of 40-60 kt cargo/passenger catamarans, trimaran, pentamaran and surface effect ship designs as well as a team design project.
Professor Latorre has also been studying the hydrodynamics of non-streamlined, box forms used for offshore structures and amphibious vehicles. At higher speeds these vessels experience bow sinkage and increased resistance. Professor Latorre received a U.S. patent No. 6,769,373.BI Aug. 6, 2004 for a bow plate that reduces barge and box shaped vessel drag and bow sinkage. This was granted on the basis of UNO towing tank tests of a 1/4-scale model of an amphibious personnel carrier M113 performed under College of Engineering sponsorship. The tank tests showed the bow plate reduced bow sinkage and achieved a 10-15% drag reduction at operating speeds. Professor Latorre is developing the bow plate under a LSU Board of Regents industrial ties grant with Mr. Dennis Herrinshaw of the UNO Office of Technology Transfer.
Dr. Latorre has also been working on fishing vessel engine emissions and fuel cells. Dr. Latorre submitted a successful proposal for Marine Engineering test engine to upgrade the NAME 3130 marine engineering laboratory. As part of the Society of Naval Architects and Marine Engineers Small Craft Committee, Dr. Latorre’s assisted in organizing the SNAME Small Craft CD released in 2004.
Recent Graduate Student Thesis: M. Pakkos (2005).Comparison of Bow Shape on Anchor Handling Tug Supply Vessel Hydrodynamics.MSc Thesis, University of New Orleans
As Anchor Handling Supply Vessels (AHSVs) operate farther offshore in deep water oil and gas fields there are a need to improve their resistance and seakeeping characteristics. Current AHSVs are built with a U-shape bow. Nevertheless published model tests have shown that adopting a V-shaped bow can result in reduced resistance and reduced Heave and Pitch responses in head seas. This paper presents the AHSV model resistance and seakeeping model test results (Fig. D) and seakeeping calculations using SHIPMO.BM software; for an AHSV with an U–form bow (UMA) and a similar AHSV with a V–form bow (VERONIKA). The results of the study showed that the V-shape bow AHSV has lower high speed resistance as well as reduced heave and pitch response in head seas. The tests showed the AHSV with the U-Form bow had smaller roll motion due to its larger linear and non linear damping.
Figure A: Test setup in UNO towing tank for model A (liftboat / crane barge) Figure B: Photograph of Bow flow at 8 knots without bow plate Figure C: Photograph of Bow flow at 8 knots with bow plate* *Note cancellation of Bow wave with Bow plate in figure C. Fig. D 2.75 m Anchor Handling Supply Vessel model with V-Shape bow in head Sea Test